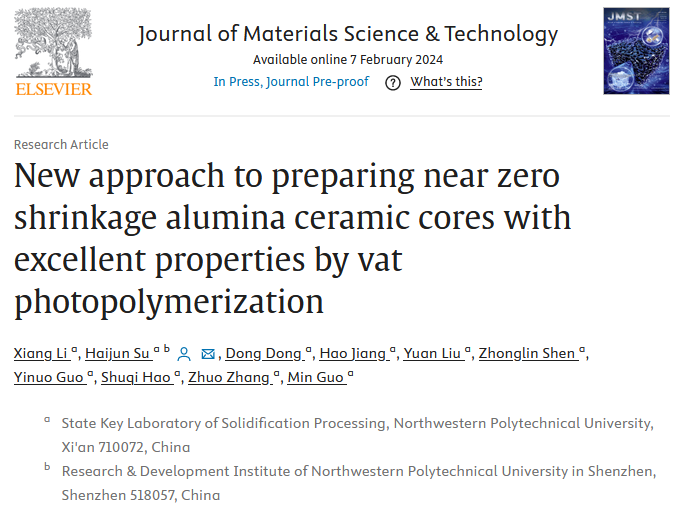
论文链接:
https://doi.org/10.1016/j.jmst.2023.12.063
成果简介
近日,西北工业大学材料学院苏海军教授团队报道了一种控制烧结气氛原位调控铝粉氧化过程的方法获得了近零收缩氧化铝基体陶瓷型芯。在研究中,作者将铝粉添加到氧化铝陶瓷芯中,通过改变从氩气到空气的气氛转换温度控制铝粉氧化发生的温度,从而调节液相烧结过程。结果发现,该方法显著改变了陶瓷型芯的微观结构并提高其综合性能。随着液相烧结时间的增加,微观结构发生了显著的粗化,并产生了一种新的晶粒形式。同时,延迟铝粉的氧化温度被证明是降低烧结收缩的有效方法,烧结收缩在X方向上达到了极低的0.3%。同时实现了高开口孔隙率(45.02%)和高抗弯强度(72.7 MPa)。该方法为调控陶瓷型芯的综合性能提供了新的思路。相关工作以题为“New approach for preparing near zero shrinkage alumina ceramic cores with excellent properties by vat photopolymerization”的研究论文发表在Journal of Materials Science & Technology(IF=10.9)。
背景介绍
随着制备技术的不断进步,3D打印技术在航空领域的应用日益广泛。其中,光固化陶瓷3D打印技术作为一种先进的制造工艺,在制备航空发动机涡轮叶片熔模铸造用陶瓷型芯方面展现出巨大的潜力和优势。航空发动机涡轮叶片是发动机中的核心部件,其性能直接影响发动机的性能和寿命。陶瓷型芯作为熔模铸造过程中的关键部件,对于涡轮叶片的制造至关重要。传统的陶瓷型芯制备方法存在着模具制作难度大、生产周期长、成本高等问题,而光固化陶瓷3D打印技术的出现,为解决这些问题提供了新的途径。光固化陶瓷3D打印技术基于数字光处理(DLP)或立体光刻(SLA)技术,通过逐层打印的方式制造出三维实体。在制备陶瓷型芯时,使用特殊的陶瓷材料作为打印材料,通过精确的光固化技术,逐层堆积形成复杂形状三维结构。整个过程自动化程度高,可以快速、准确地制造出复杂形状的陶瓷型芯。
相比于传统制备方法,光固化陶瓷3D打印技术具有以下优势:1. 高精度与复杂形状制造能力:能够制造出具有复杂内部结构和精确尺寸的陶瓷型芯,满足涡轮叶片的精密铸造要求;2. 缩短生产周期:大幅减少了模具制作和后处理的时间,加快了产品迭代速度。3.降低成本:简化了生产流程,减少了原材料浪费,降低了生产成本。4. 优化设计灵活性:可以根据实际需求快速调整陶瓷型芯的设计,实现定制化生产。
然而,光固化陶瓷3D打印技术在制备航空发动机涡轮叶片熔模铸造用陶瓷型芯方面仍面临一些挑战。例如,陶瓷材料的可打印性、打印过程中的精度控制、后处理工艺的优化等。为了充分发挥光固化陶瓷3D打印技术的优势,还需要在材料、设备、工艺等方面进行深入研究和改进。其中,后处理过程中较高的收缩率对于陶瓷型芯的缺陷及成形精度具有重要影响。烧结收缩较高容易在陶瓷型芯中引入应力进而产生开裂缺陷,另外,体积收缩造成形状及尺寸精度难以控制。因此,降低陶瓷型芯3D打印过程中的收缩率对抑制缺陷,提高产品精度和性能具有重要的意义。
图文导读
一、气氛控制铝粉原位氧化方法
结合图1和图2,确定铝粉及树脂脱脂过程中的关键温度,制定脱脂和烧结制度,分别控制铝粉在500°C,600°C,1000°C,1400°C和1600°C进行氧化,关键特征温度如表1所示。结果表明在500°C时基本不发生氧化,600°C发生了部分氧化,1000°C以上铝粉完全氧化,证明实验设置的脱脂和烧结制度可以控制后处理过程中铝粉的原位氧化过程。
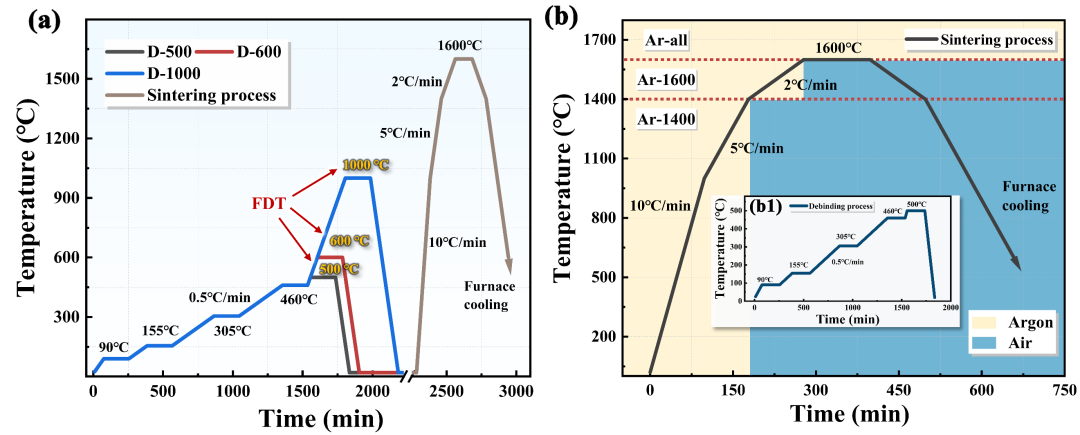
图1. 光固化3D打印陶瓷型芯的后处理过程:(a)控制脱脂最终温度为500°C,600°C和1000°C,烧结全过程为大气气氛;(b)烧结升温至1400°C,1600°C时将气氛由氩气保护转变为大气气氛
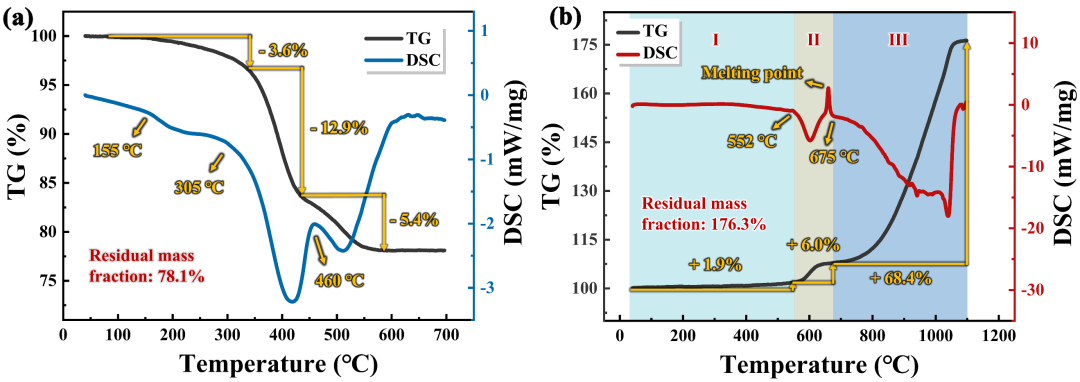
图2. (a)光固化3D打印陶瓷型芯STA结果;(b)大气气氛下铝粉的STA曲线
表1: 不同后处理制度的特征温度
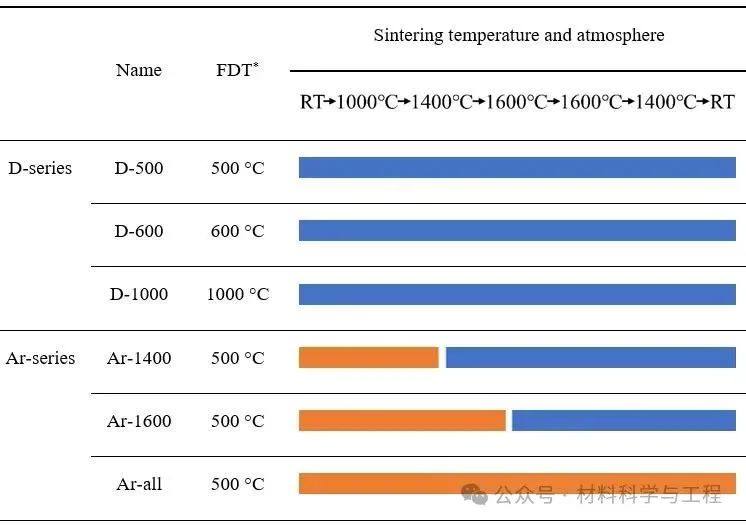
二、显微结构特征
图3和图4分别证明了光固化3D打印氧化铝陶瓷型芯的显微结构在不同的后处理制度以及不同的铝粉添加量下产生了明显的变化。添加铝粉并且在高温下氧化会在烧结过程中产生液相,形成一种新的团聚颗粒,降低体系的表面能,进而降低烧结收缩。
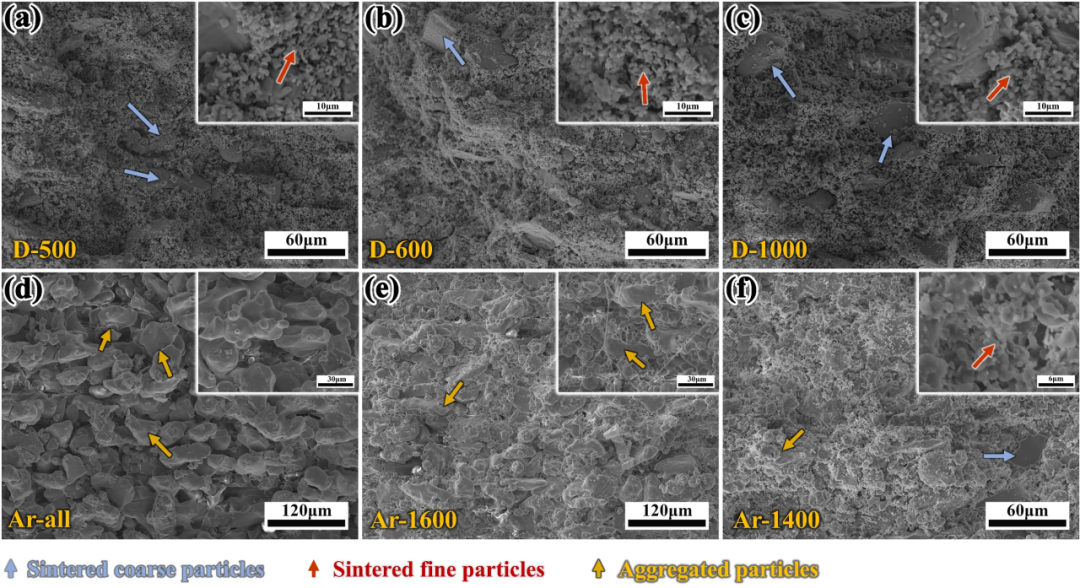
图3. 添加15wt.% 铝粉的陶瓷型芯在不同后处理制度下的显微结构:(a) D-500; (b) D-600; (c) D-1000; (d) Ar-all; (e) Ar-1600; (f) Ar-1400.
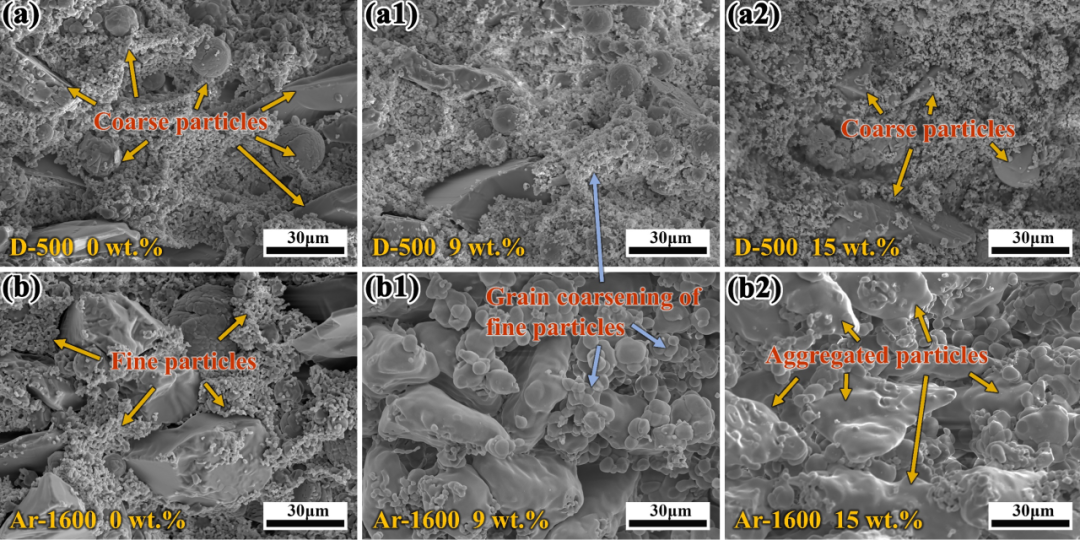
图4. D-500和Ar-1600后处理制度下不同铝粉添加量的光固化3D打印氧化铝陶瓷型芯显微结构:(a)0 wt.% Al, D-500; (a1) 9 wt.%Al, D-500; (a2) 15 wt.% Al, D-500; (b) 0 wt.% Al, Ar-1600; (b1) 9 wt.% Al,Ar-1600; (b2) 15 wt.% Al, Ar-1600.
三、组织演变行为分析
添加铝粉的陶瓷型芯在脱脂后铝粉并没有发生明显的氧化,当烧结温度升至1400°C或1600°C后,铝粉在氩气气氛下不会发生氧化,但是会由固态向液态转变,并在表面张力的作用下形成团聚颗粒。延长液态铝作用时间或增加液态铝的含量会提高团聚颗粒的数量。
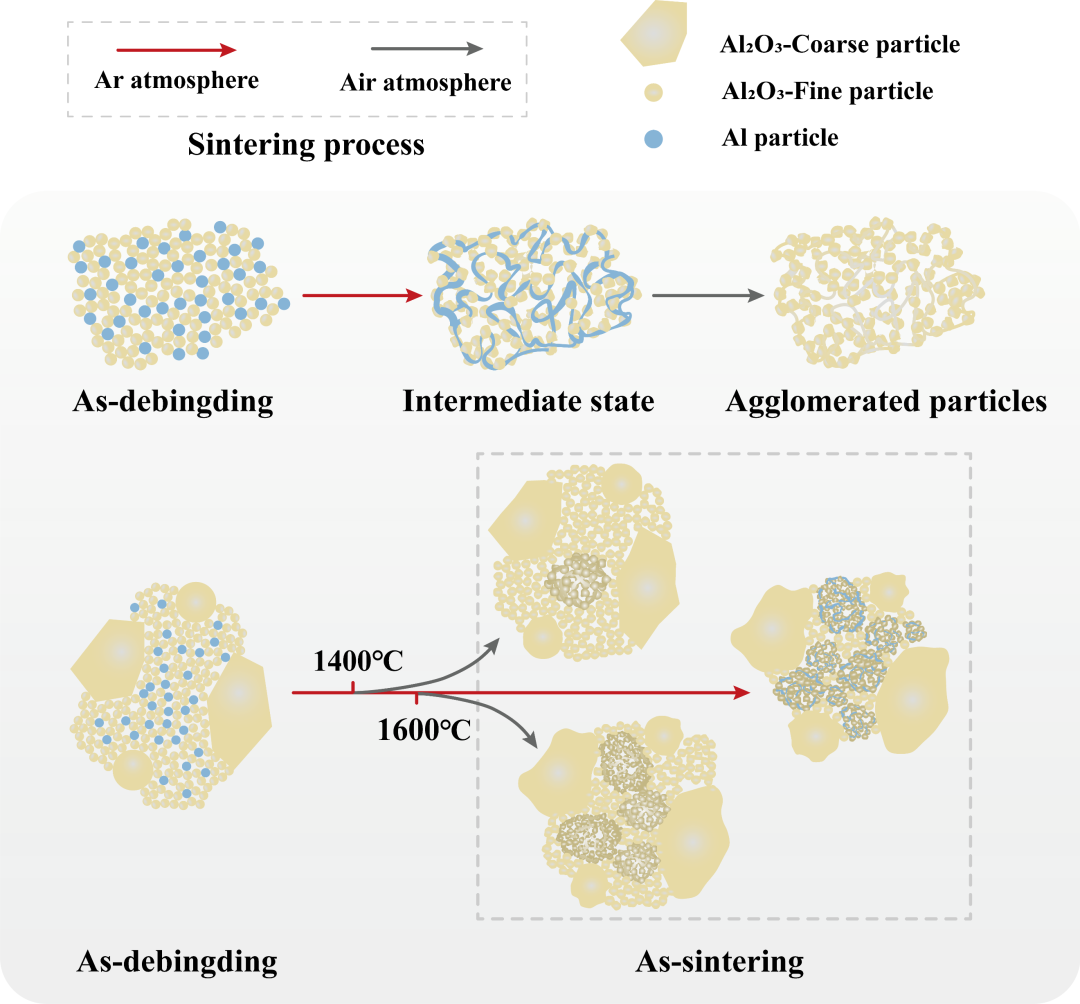
图5. 铝粉增强氧化铝陶瓷型芯组织演变示意图
四、陶瓷型芯综合性能
本研究通过气氛控制铝粉原位氧化新方法,获得的陶瓷型芯具有较高的综合力学性能。烧结收缩在X方向上达到了极低的0.3%,同时实现了高开口孔隙率(45.02%)和高抗弯强度(72.7 MPa)。
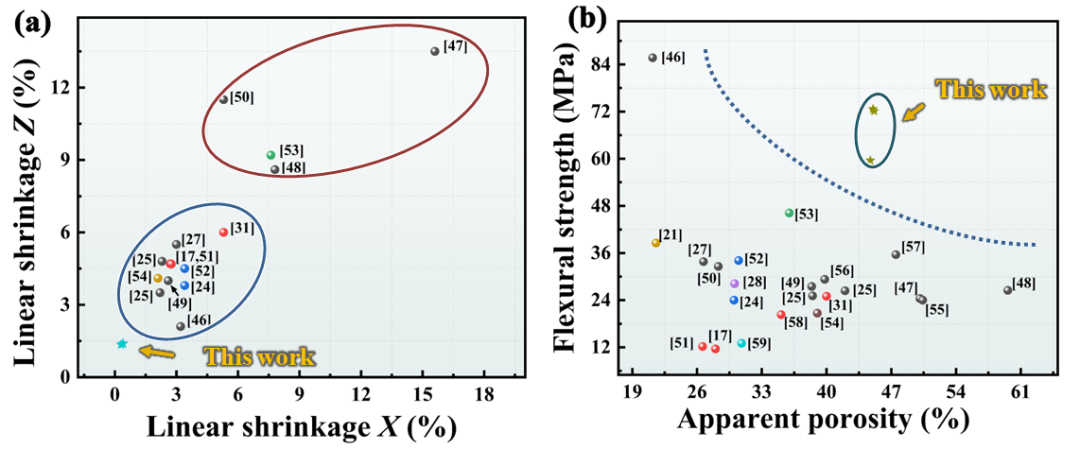
图6. 光固化3D打印陶瓷型芯性能对比
结论与展望
综上所述,本研究提出了一种巧妙的方案:通过气氛控制铝粉原位氧化,解决了3D打印氧化铝陶瓷型芯烧结线性收缩率高的问题。将细铝粉添加到陶瓷芯中,细铝粉能够增加体系的表面能,促进烧结收缩,而铝粉氧化则减少烧结收缩。我们通过控制烧结气氛,创造性地延迟铝粉的氧化过程,实现了显微结构和性能的调控。陶瓷型芯的相组成和显微结构证明了该方法的有效性,新生成的团聚颗粒是陶瓷型芯微观结构演变和性能优化的关键。此外,孔结构分析表明,气氛控制的液相烧结有利于增加孔的尺寸和体积,这是提高氧化铝基陶瓷型芯溶出性的一种理想结构。烧结收缩在X方向上达到了极低的0.30%。同时实现了高显孔隙率(45.02%)和高抗弯强度(72.7 MPa)。本研究发展的创新方法为调控陶瓷材料的微观结构和性能提供了一条新途径。
通讯作者简介
苏海军
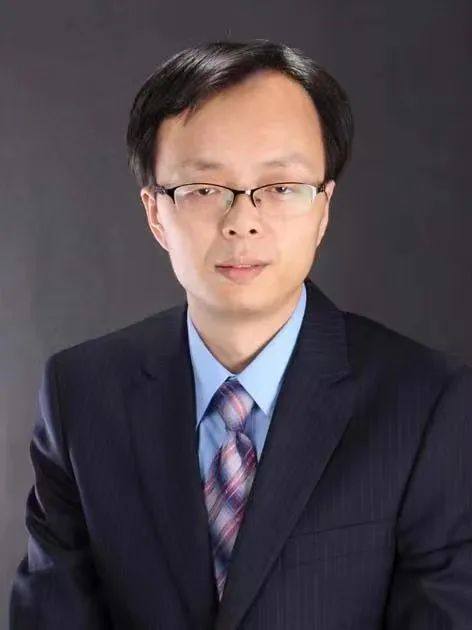
西北工业大学材料学院教授、博士生导师。国家“万人计划”科技创新领军人才,国家优秀青年科学基金获得者,中国有色金属创新争先计划获得者。长期从事先进定向凝固技术与理论及新材料研究,涉及高温合金、超高温复合陶瓷、半导体复合材料、有机薄膜太阳能电池、生物医用陶瓷材料,以及定向凝固和激光增材制造技术与理论等。主持包括国家自然基金重点、优青等7项国家基金在内的30余项国家及省部级重要科研项目,在Nano Energy,Advanced Functional Materials,Nano Letters,Composites part B: engineering,Additive manufacturing等众多知名期刊发表SCI论文160余篇。获授权中国发明专利50项以及2项美国发明专利。参编专著3部。
原文始发于微信公众号(材料微生活):材研资讯 | 苏海军教授团队JMST:实现3D打印陶瓷型芯近零收缩!