随着节能减排要求的提高以及汽车电动化的加速,汽车轻量化成为汽车行业的发展潮流,推动着包括高强度钢、铝合金、工程塑料以及复合材料等在内的轻量化材料在汽车领域的应用。连续纤维增强热塑性复合材料(CFRTP)作为一种高强度、高刚性、高韧性、可回收的新型热塑性复合材料,与钢、铝合金相比,可以有相当的强度、重量更轻、能量吸收能力更高;与热固性复合材料相比,更易于加工,且环保可回收,在汽车轻量化设计中具有巨大的应用潜力,可替代部分金属材料和高端聚合物材料,应用于座椅靠背、前端模块、车门内板、保险杠等车身结构件、半结构件上。
名称 | OEM | 原材料 | 效益 |
座椅底板 | 通用欧宝Astra OPC | 巴斯夫 Ultramid™ | 生产出的座椅底板减轻了45%的重量 |
独立后排座椅外壳 | 奥迪A8 | 朗盛 Tepex® Dynalite | 与钢板相比,重量减轻45% |
座椅靠背骨架 | 上汽概念车 | 巴斯夫 Ultracom™ | 重量与传统座椅相比减轻达20%,轻薄设计更为第二排乘客增加2.5厘米的膝部空间 |
越野车后排座椅 | | 朗盛 Tepex® Dynalite | 质量比类似钢结构轻40%以上,同时可承受加速载荷的撞击 |
前端模块 | 大众Atlas和Teramont | 朗盛 Tepex® Dynalite | 比用钢板制成的嵌件约轻50%,CFRT嵌件区域可以承受更高的应力 |
轻量化A柱 | 保时捷 | 朗盛 Tepex® Dynalite | 重量减轻了5kg |
SUV前端支撑 | 梅赛德斯—奔驰GLE SUV | 朗盛 Tepex® Dynalite | |
车门基板 | 福克斯 | 金发科技 | 与钢材及长纤维PP门系统相比,热塑性复合材料门系统相对减重大于30% |
发动机底盘 | | 朗盛 Tepex® Dynalite | 重量比同等的钢材组件轻了60%以上,比相应的铝部件轻20%以上 |
悬架控制臂 | PSA标致 | | 重量减轻了50% |
刹车踏板 | 保时捷、宾利欧陆GT | 朗盛 Tepex® Dynalite | 重量仅有传统钢制踏板的一半左右 |
侧门防撞梁 | PSA标致雪铁龙 | 杜邦 Vizilon™ | 与超高强度钢(UHHS)相比,重量减少40%,能吸收更多的冲击能量 |
消声器隔热罩 | 宝马i8 | 朗盛 Tepex® Dynalite | 确保部件在高温环境中不发生变形或失效,提高部件在冰冻温度下的强度和抗冲击性能 |
车轮觳插片 | 蔚来ES8 和ES6 | 科思创 Maezio™ | 外观优质,稳定性好 |
除了上述应用外,随着技术的发展成熟,连续纤维增强热塑性复合材料正越来越多地被用作汽车轻量化设计中金属的替代品。下面我们来看看,近期连续纤维增强热塑性复合材料在汽车上的创新应用。
一、宝马ix前围板和后窗框架部件
早在2010年,宝马集团就在JEC World展会期间公布了其首款大量采用复合材料的电动乘用车,而在后面的i3、i8、7系设计中同样大量采用了碳纤维复合材料。宝马iX则是宝马集团在大量采用复合材料的全电动设计方面取得的又一进展,在iX中,宝马集团整合了7系的Carbon Core与之前宝马i 系的全碳纤维的车身结构,它采用了多材料的车身结构,宝马集团将这种车身结构称作Carbon Cage。侧框架、雨水槽、车顶框架、前围板和后窗框架的 CFRP 部件组合形成一个“Carbon Cage ”,在加固车身的同时,减轻重量并提高车辆的灵活性。而前围板和后窗框架部件采用全新方法由连续纤维增强热塑性塑料 (CFRTP) 制成。
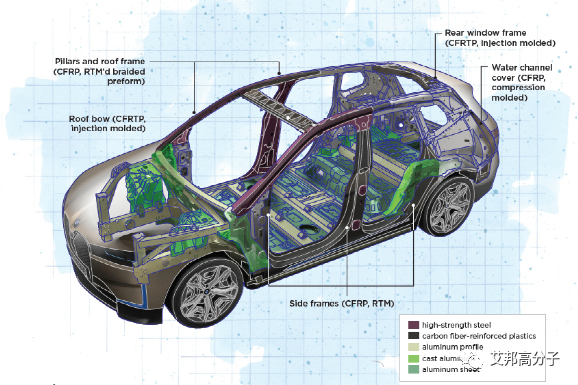
这种CFRP-CFRTP的混合结构与同样的钢制部件相比,在提高刚性的同时还减轻了5 kg的重量,同时实现了宝马想要的简约外观,从而增加了乘员舱的宽敞感。
二、奔驰S级轿车驾驶辅助系统电池支架
在梅赛德斯-奔驰 S 级轿车的高级自动化驾驶辅助系统结构件中,采用朗盛Tepex® 连续纤维增强热塑性复合材料制造电池支架,为该系统的“智能驾驶”供电。据介绍,这款弓形支架由德国洛恩的Poeppelmann Kunststoff-Technik 公司制造,它的基材为聚丙烯基 Tepex® dynalite 104-RGUD600(4)/47%,制造方法是将复合材料的成型(悬垂)与注射成型相结合的两步法工艺。采用复合材料可以使成品可比金属造的减重 40%,注塑成型步骤还可实现集成功能,不仅使安装支架变得更加容易,而且还可减少了传送运输工作。这些加工工艺有助于降低制造成本。且复合材料对车身和电池的金属部件是电绝缘的,大大降低了短路的风险。而由金属制成的组件需要额外的措施来防止短路。三、梅赛德斯-奔驰S级轿车上的负载舱
朗盛Tepex dynalite连续纤维增强热塑性复合材料的一项新应用是制造安装在梅赛德斯-奔驰S级轿车上的负载舱,用于容纳 48V 车载电源电池。这种复合材料部件能够承受高机械应力,并且比同类金属板部件轻30%左右,可以防止电池在发生碰撞时穿透或损坏凹槽壁,同时确保负载舱的密封性。
该部件采用混合成型工艺,坯料由基于聚酰胺6的Tepex dynalite 102-RG600(2)制成,并用两层连续玻璃纤维织物增强。朗盛的 Durethan 聚酰胺6用于注塑紧固件和加强筋。除了S轿车外,Tepex dynalite还应用于梅赛德斯-奔驰 C 级轿车的负载舱,用于容纳车载电源电池。轻质结构材料比金属轻得多,未来将在电动汽车安全装置、完整的电池系统外壳或引擎下可用的装载空间组件方面有巨大应用潜力。四、东风汽车轻型卡车工具箱
SABIC与中国主要货车制造商东风汽车合作,开发出一种用于生产坚固而且轻量化的车载工具箱新型复合塑料混合解决方案。该应用混合了SABIC的 STAMAX™ 长玻纤聚丙烯树脂和一种连续玻纤复合层压嵌件,采用双色注塑工艺生产。与类似设计的钢制零件相比,采用该方案生产的成品零件重量减轻了30%,并有效提高了东风汽车的生产效率。SABIC的混合解决方案结合了 STAMAX 树脂与热成型复合嵌件,这款嵌件由连续玻纤增强热塑性复合材料生产商江苏奇一科技生产的单向玻纤增强聚丙烯带制成。层压嵌件在放置入模具之前需进行预热,并在一次操作中与 STAMAX 树脂一同进行双色注塑成型。这一嵌件可提高零件关键区域的刚度和强度,从而实现薄壁几何设计,以此减轻零件重量。采用塑料复合解决方案生产的卡车工具箱重量减轻了约 30%(4-6kg),同时保证了应用所需的刚度、韧性和强度。综上,高性能、低密度的连续纤维增强热塑性复合材料已成为汽车轻量化中极具潜力的材料之一,在汽车半结构、结构件上广泛应用。从材料上看,国外连续纤维复合材料产业日趋完善,应用相对成熟,而国内相关企业的产品也逐步得到汽车制造商的认可。从工艺上来看,大批量自动化,以及多工艺材料的复合生产技术,符合未来汽车行业轻量化与集成化设计的发展趋势。原文始发于微信公众号(艾邦高分子):盘点连续纤维增强热塑性复合材料在汽车上的应用